Technology for transmitting commands through pipeline walls
During the operation of oil and gas pipelines, it is regularly necessary to communicate with devices located inside the pipeline. Data exchange with inline equipment is used to track cleaning pigs and inspection tools during cleaning and inspection work, to control inline dock shelters during repair work, etc.
At the same time, receiving a signal from an inline shell located inside a thick-walled metal pipeline is associated with great difficulties. First, communication is impeded by the limited penetration of an alternating magnetic field into the metal walls of the pipeline, and secondly, by electromagnetic interference generated by industrial equipment.
Currently, low-frequency transmitters are widely used for signal transmission from in-line equipment. Most transmitters operate at 21-23 Hz. The choice of such an operating frequency is due to a compromise between the degree of signal penetration, its transmission rate and signal noise immunity. At lower frequencies, data exchange takes an unacceptably long time, and as the frequency increases, the signal in a metallic environment quickly decays (shields). In addition, when approaching industrial frequencies of 50-60 Hz, the level of interference increases sharply, degrading the quality of communication.
Despite these difficulties, the technology for detecting in-line pigs is currently quite well-established. In practice, the most commonly used set of low-frequency transmitter and 22Hz locator . < / p>
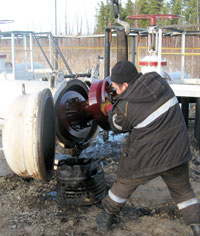
But often this functionality is not enough. Here's a typical example. A pig with a low-frequency transmitter is stored in the launch chamber and the chamber is pressurized. At this time, for some reason, a team comes to cancel the work. You can, of course, leave the pig in the chamber until waiting for the launch command, but the transmitter inside the pig is already emitting a signal, consuming energy. If the waiting time is long or unknown, you will have to relieve the pressure, drain oil from the launch chamber, open the chamber lid and remove the stored pig to replace the batteries on the transmitter. And after that, you still need to re-stock the pig. This work is very time consuming.
Unproductive loss of time and resources can be significantly reduced if it is possible, after re-supplying, to send to the inline equipment a command to turn off and turn on the low-frequency transmitter without removing the pig from the chamber . The specialists of APRODIT LLC are working on the improvement of the transceiver , controlled through a thick-walled pipeline.
Development of a low frequency transceiver
The main task that our specialists solved when developing a low-frequency transceiver was to achieve stable command transmission against the background of electromagnetic interference. The technology was developed on the basis of a well-mastered technique for detecting a low-frequency transmitter in a pipeline. The technology is based on the algorithm amplitude-phase keying (AFM) of electromagnetic signals of ultra-low frequency 22 Hz, developed by LLC "APRODIT". To increase the noise immunity of control, methods of accumulation and filtering of the received signal, duplication of transmitted information and confirmation of the received command are used.
Currently, the onboard (installed on the cleaning piston) PPNT-00 transceiver has been brought to the stage of industrial application. New onboard transceiver functions - go to sleep and wake up on a command transmitted at 22 Hz from an external transmitter outside the pipeline .
If it is necessary to save the energy resource of the onboard transceiver located in the launch chamber, it is put into sleep mode by a command from an external transmitter. The transition to the lowest power consumption mode (sleep mode) is controlled by a low frequency locator located near the launch camera. In sleep mode, the transceiver can be in the launch chamber for several days or even weeks, with virtually no reduction in further operation time. Before launching the pig, it is necessary to wake up the onboard transceiver from sleep mode with a command from an external low-frequency transmitter. The control of turning on the transceiver is carried out by the presence of a signal on the locator located outside the camera. After that, you can launch the pig.
Algorithm for controlling the PPNT-00 transceiver
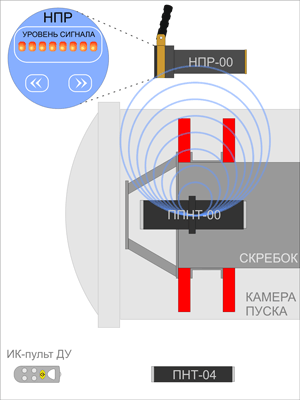
Figure: 1. On-board transmitter in radiation mode.
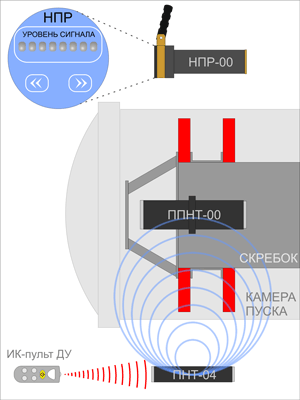
Figure: 2. Putting the on-board transmitter into sleep mode.
- PPNT-00 - onboard low-frequency transceiver
- PNT-04 - auxiliary external low-frequency transmitter
- IR remote control - infrared remote control
- NPR-00 - low-frequency locator
- PPNT-00 - onboard low-frequency transceiver
- PNT-04 - auxiliary external low-frequency transmitter
- IR remote control - infrared remote control
- NPR-00 - low frequency locator
Preparing the pig for launch .
- The PPNT-00 transceiver is switched on in the radiation mode "in batches" (periodic signal) using the IR remote control. Radiation monitoring is carried out using the NPR-00 locator: the indicators on the locator panel are on. PPNT-00 is installed on a pig, which is placed in the launch chamber.
- After closing the camera, it becomes impossible to control PPNT-00 using the IR remote control. The NPR-00 locator continues to record the signal emitted by PPNT-00 (see Fig. 1).
Enables hibernation .
An additional PNT-04 transmitter is required to switch to sleep mode.
- The PNT-04 transmitter is located parallel to the on-board transceiver at a distance of 1-2 meters from the launch chamber.
- The IR remote control sends a command to the PNT-04 transmitter to turn on the sleep mode on the PPNT-00 onboard transceiver (see Fig. 2).
- The PNT-04 transmitter transmits the command to enable the sleep mode at a frequency of 22 Hz (see Fig. 2) and turns off.
- The PPNT-00 transceiver, having received a command from the PNT-04, goes into sleep mode and stops emitting a signal.
- The PPNT-00 transceiver, having received a command from the PNT-04, goes into sleep mode and stops emitting a signal.
Wake up from sleep .
- The PNT-04 transmitter is located parallel to the on-board transceiver at a distance of 1-2 meters from the launch chamber.
- The IR remote control sends a command to the PNT-04 transmitter to wake up the PPT-00 onboard transceiver from sleep mode.
- The PNT-04 transmitter sends a command to wake up from sleep mode at a frequency of 22 Hz and turns off.
- The PPNT-00 transceiver, having received the command from the PNT-04, switches to the "packets" mode of radiation. Radiation monitoring is carried out using the NPR-00 locator.
After turning on the transceiver in the radiation mode, you can launch the inline shell. To prevent PPNT-00 from accidentally turning off while moving through the pipeline due to interference, it has a built-in motion sensor , which makes it impossible to switch to sleep mode while moving along the pipeline.
Currently, APRODIT LLC is working on introducing the function of transmitting an amplitude-phase-shift keyed signal into the NPR-00 low-frequency locator. In this case, commands to the PPNT-00 onboard transceiver can be sent directly from the modified NPR-00 locator without an additional PNT-04 low-frequency transmitter.
Possibilities and limitations of information transmission technology through metal walls.
As noted above, transmitting even the simplest commands at a frequency of 22 Hz through thick metal walls against a background of various electromagnetic interference is not an easy task. Low frequency transmission technology has several limitations. In terms of the complexity and duration of the signal transmission, it can be compared with the control of the Lunokhod from the Earth. The data transfer rate through metal walls is extremely slow. It takes a few seconds to transmit one command and confirm its receipt. There are several reasons for this delay. First, the low frequency of the carrier signal - only 22 oscillations per second. Secondly, between the reception and transmission of the signal, there must be a pause for the damping of oscillations in the transmission-receiving antenna path. Third, the signal can be disrupted due to external interference, and duplication of the command is required. As a result, the typical time for transmitting one command at a frequency of 22 Hz and confirming its receipt takes about a second. And against the background of strong electromagnetic interference - up to ten seconds. Therefore, during the transmission of a command, both devices must be motionless relative to each other . It is not worth relying on the exchange of information between a stationary transmitter located on the surface and an inline shell, which travels at a speed of 5 m / s through the pipeline.
The low-frequency transceiver is capable of transmitting or receiving through the metal wall of the pipeline only a limited set of simple commands and signals. In the vast majority of cases, this is quite enough. For example, you can find out the charge level of the batteries or send the on-off status for any subsystem of the inline tool.